Recondition, Overhaul or Rebuild my Plate Heat Exchanger
Reconditioning a gasketed plate heat exchanger involves the steps below. A quality-factory-certified reconditioning will ensure minimized downtime and disruption to your operations. We service any make or model of plate heat exchangers.
The steps involved:
- Inspecting the unit for external leaks, internal leaks (cross contamination),
- Checking the correct tightening dimension (A-dimension),
- Opening the unit, removing gaskets in nitrogen tank,
- Cleaning plates in acid and caustic baths,
- Liquid-penetrant-testing (LPI) of plates for cracks and holes,
- Attaching gaskets using two-part epoxy, oven-curing,
- Rebuilding the unit as per the plate-hanging list,
- Tightening to the A-dimension
- Hydro-testing to the design pressure.
The process ensures your gasketed plate heat exchanger continues to perform as designed and that the energy losses are minimized over the lifetime of your plate heat exchanger.
Recondition a Plate Exchanger (Any make, Any model)
Reconditioning your Heat Exchangers at one of our Canadian facilities to bring your equipment back to its original performance. Using Alfa Laval Reconditioning Services ensures that the equipment performs and is as reliable as the original manufacturer's specifications.
Alfa Laval's workshops are located in Alberta and in Ontario. We recondition, overhaul, rebuild and repair your heat exchanger according to your specific needs, summarizing our activities in a report once the work is completed.
Our state-of-the-art Alfa Laval Service Centres, which use the latest technologies and environmentally sound processes, provide the same high quality of service regardless of location.
Watch a short video guide through the important steps of our reconditioning of a heat exchanger.
How are heat Plate Heat Exchangers reconditioned?
The following steps are followed in a quality controlled process:
- A visual Inspection on arrival
- The unit is opened and another visual inspection of the frame components for any corrosion or erosion and individual plates are visually inspected and if need be measurements are made to determine the level of deformation. Plates with unacceptable deformation need replacing
- Gaskets are removed in a liquid nitrogen bath, a gentle and thorough removal without the possibility of damaging the plates
- Plates are cleaned in acid and caustic baths to remove all fouling and scaling without damaging the plates
- Liquid-Penetrant-Inspection (LPI) for cracks and holes to check the integrity of the plates
- Gaskets are either clipped on or bonded with factory approved two-part epoxy glue and oven-cured.
- Alfa Laval specified materials are used throughout the reconditioning process
- Using factory-approved tightening devices to close the unit to the right specification
- Hydrostatic test and visual inspection as a final check
Let Alfa Laval reduce maintenance costs over the lifetime of your heat exchangers.
Ten Top Tips to Keep your Plate Heat Exchanger in Tip Top Condition
- Make sure that the operating conditions (temperatures and flow rates) comply with the design specifications.
- At start-up, vent the heat exchanger but open and close the valves slowly to avoid pressure surges and water hammer.
- Use upstream filters and strainers to remove particulate fouling and protect the heat exchanger.
- On a daily basis check for any changes in temperature or pressure and check for any signs of external leaks.
- On a regular basis keep the tightening bolts clean and well-lubricated.
- Use Performance Audit to avoid having to open the plate heat exchanger for inspection.
- Use Cleaning-In-Place (CIP) to avoid the need to open the heat exchanger for cleaning.
- Always keep stand-by units clean and dry. If a heat exchanger is taken out of service, flush with fresh water and drain it completely.
Protect heat exchangers from water splash and rain. Avoid exposure to ultraviolet rays and ozone typically generated from electrical sources.
- Only use genuine spare parts for guaranteed performance, reliability and equipment life. Maintain a stock of essential spare parts and follow the storage instructions.
We have service and parts for any make, any model, of Plate Heat Exchangers!
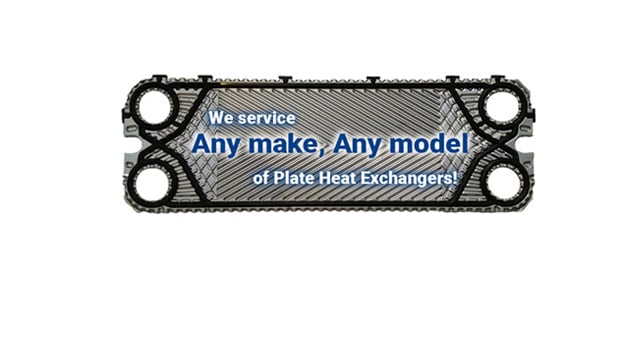
Contact Service and Parts
Toll free: +1 888 253 2226 (888-ALFACAN)
Service and Parts: canada.parts@alfalaval.com
Equipment Inquiries: alfacan.info@alfalaval.com
24/7 and Field Service
+1 888 253 2226
Alfa Laval Subject Expert: Gina Smith
Field Services Coordinator Ext. 343
Email us a Field Service Question
Service Centre (Eastern Canada)
Phone: +1 416 299-6101
Fax: +1 416 297-8690
101 Milner Avenue
Scarborough, Ontario
M1S 4S6, Canada
Service Centre (Western Canada)
Phone: +1 780 413-6349
Fax: +1 780 450-6747
6344 Roper Road
Edmonton, AlbertaT6B 3P9, Canada
Download
Downloads
Don’t make the non-OEM mistake.
Studies show that 88% of all processors have experienced equipment failure with non-OEM parts. Don’t risk uptime and productivity with bad spares.
Remember, look for the logo. Buy genuine parts.
How long will your gaskets last?
Using Alfa Laval’s proprietary GPredict™ tool, our service advisors can give you a reliable estimate of the expected lifetime of your gaskets. The tool relies on precise calculations based on your specific equipment and relevant application details, including temperature, gasket material, whether you use glued or non-glued gaskets, and how often you open your unit in the course of annual operation.
Alfa Laval’s services advisors will also consider the operating pressure of your duties,
in order to give you a detailed assessment of the leakage risk. This helps you avoid unplanned stops and preventable safety risks in the course of your production.
GPredict™ is a powerful tool that makes it simple to plan the reconditioning of your plates, since you always know when it’s time for regasketing well in advance. Take advantage of GPredict™ with a customized gasket prediction based on your installation* by contacting us today.