Energy efficiency opportunities around different heat exchanger positions in a fractionator – Part 1
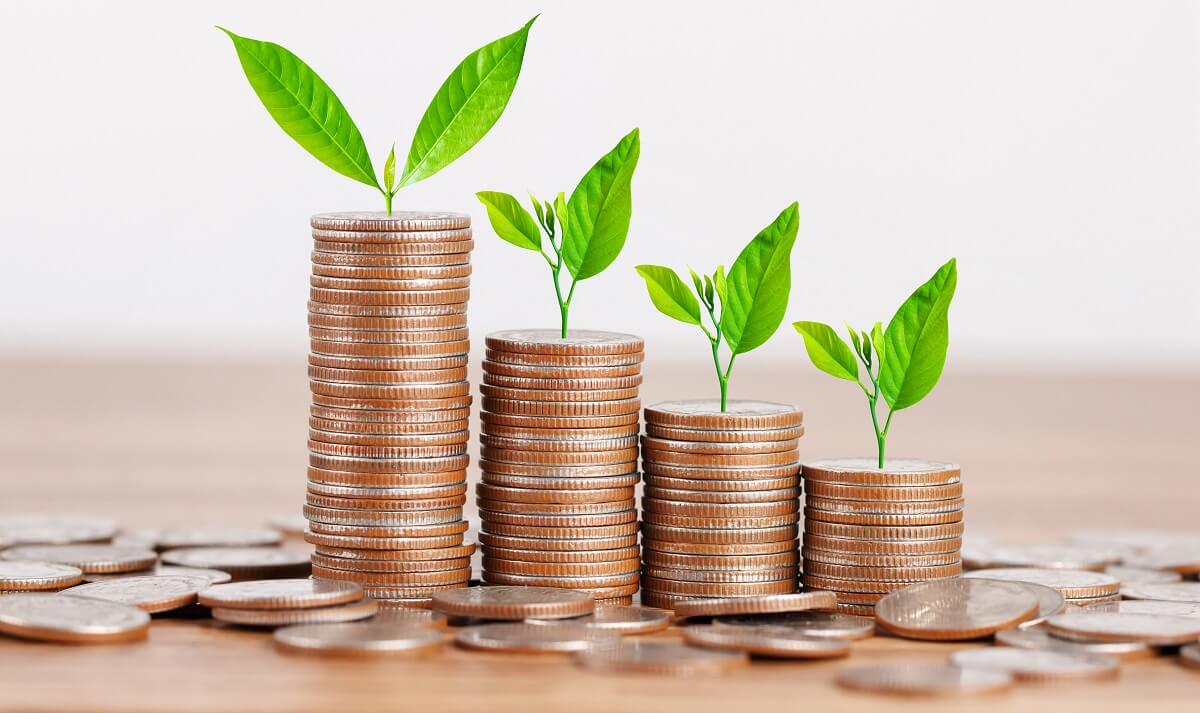
As mentioned in our previous blog post on scope 1, 2 and 3 emissions, an essential first step towards reducing carbon footprint and making a profit is identifying and evaluating the right energy efficiency opportunities that make the most business and economic sense.
There are essentially two approaches a refinery can take to improve energy efficiency:
- Strategic approach: The refinery consciously develops projects focusing on energy efficiency which becomes one of the key performance indicators of a process unit or a project investment (grass root or revamps). Our post on Alfa Laval's Energy Dome concept is one example of this approach.
- Opportunistic approach: The refinery takes a more holistic approach by evaluating areas where they already plan to spend money, such as unit safety and reliability purchases. Examples include bundle replacement, metallurgy upgrades, heat exchanger end of life or small improvement projects.
In this post, we will focus on the areas of improvement available via the opportunistic approach.
Opportunistic approaches to energy efficiency
There are four main areas of focus when utilizing an opportunistic approach:
- Fractionator overhead condenser
- Feed/Bottoms interchanger
- Product coolers
- Reboilers
Let’s dive deeper into each of these areas.
Energy efficiency opportunities around fractionator overhead condenser
Fractionator overhead (e.g., CDU, FCC, Coker, Hydrotreaters, Alky, Gas plant) is an important position to look at for energy efficiency opportunities. Traditionally overhead positions have been overlooked as a candidate for energy efficiency; limited by century-old shell-and-tube technology and the rule of thumb. However, with the availability of Compabloc welded plate heat exchanger, overheads are becoming a favorite solution.
There are various ways we can look at overheads to harness energy efficiency:
- Waste heat recovery: Recovering waste heat to process fluid or boiler feed water instead of rejecting heat to atmosphere (air coolers) or cooling water.
- Reduce pressure drop: Thereby reduce column operating pressure and reboiler duty which can also help improve fractionation efficiency.
- Reduce cooling water consumption: For water-cooled condensers, we can reduce cooling water flow required by 50% by doing a temperature cross.
- Maximize sub-cooling/condensing: This can improve product recovery and reduce off-gas compressor duty.
Energy efficiency opportunities around feed/bottoms interchanger
In most cases, the fractionator or stripper feed needs to be heated up before entering the column to aid the separation of different fluids with the help of heat.
There are two ways heat is input into the column:
- Reboilers
- Preheating the feed
In most modern fractionator column designs, feed is preheated by column bottoms, which is already a very good concept of energy recovery. However, heat recovery in feed to bottom exchangers has been limited by conventional shell-and-tube technology.
To recover more heat from the column bottoms to the feed, an excellent tool to use is a cross-temperature approach, forcing the cold fluid outlet temperature to be higher than the hot fluid outlet temperature. To achieve a cross temperature in shell-and-tube technology, we need to use multiple shells in series.
Unfortunately, you can put only so many in sequence before it makes no economic sense, considering the total footprint and installed cost. However, the rules change when we consider deploying welded plate heat exchanger technology, which can achieve a deep temperature cross in a single Compabloc shell and compact footprint by replacing multiple shells in the series.
The benefits of a deep temperature cross and higher heat recovery than traditional feed to bottoms exchanger design can lead to both CapEx and OpEx savings. Higher feed temperature in the column can reduce the size and duty of the reboiler, reducing reboiler steam consumption. Also, higher heat exchanged to feed means colder bottoms or product leaving the interchanger, reducing the size and duty of downstream product air coolers or water coolers, reducing electricity and/or water consumption.
Some of the most common feed to bottom interchanger applications in refineries where Compabloc welded plate heat exchanger technology is applied are:
- ARU/SRU unit: Lean/Rich amine interchanger
- SWS unit: Sour/Stripped water interchanger
- Hydrotreater unit: Stripper feed/bottoms interchanger | Reactor feed/effluent exchanger
- ISOM unit: Stabilizer feed/bottoms interchanger
- Alkylation unit: DIB feed/bottoms exchanger | Reactor feed/effluent exchanger
Energy efficiency opportunities around product coolers
Fractionation columns can have multiple product streams leaving the fractionation column, such as through the fractionation bottoms, overhead condensate and side cuts, to name a few, and need to be cooled down before moving to tankage. Based on the temperature of the product stream, cooling media availability and footprint availability, these products can deploy either of these cooling methodologies before going to storage.
Hot product -> Air coolers -> Product storage
Hot product -> Air coolers -> Water trim cooler -> Product storage
Hot product -> Water cooler -> Product storage
Product coolers are the last areas of opportunity for energy efficiency, yet there is enormous potential to apply energy efficiency concepts. Two of the most commonly used concepts deployed using Compabloc welded plate heat exchanger technology are:
- Waste heat recovery: Recovering waste heat to process fluid or boiler feed water instead of rejecting heat to atmosphere (air coolers) or cooling water.
- Reduce cooling water consumption: For product water coolers or trim coolers, we can reduce the cooling water flow required by 50% by doing temperature cross.
Energy efficiency opportunities around reboilers
Reboilers and their design play a vital role in a properly functioning fractionation column. The reboiler's main job is to provide heat to the column by boiling liquid bottoms and returning vapors or mixture to the column. Sometimes, it also acts as a theoretical separation staging area. The most common heat sources for reboilers are steam, hot oil and fired heater.
Below are a few energy efficiency deployment options for reboilers using Compabloc heat exchanger technology:
- Low-grade steam: Steam reboilers using shell-and-tube technology are traditionally designed with an extensive MTD between steam and the boiling media. Compabloc can run efficiently with very close temperature approaches bringing down MTD significantly and opening up the possibility of using low-grade steam. This shifts from high-value HP steam to MP steam or MP steam to LP steam.
- Using low-grade process heat: Tighter MTD using Compabloc technology allows low-grade process heat (products/overhead vapors/slipstream from reactor effluents, etc.) to run the reboiler, displacing expensive utilities like steam/hot oil or fired heater.
Fractionator heat exchanger positions can meet many needs at once
As you can see, many options are available to help you meet your sustainability goals. Engaging a company such as Alfa Laval and utilizing their refinery experts' know-how and experience to help you identify the opportunities in your refinery will yield the most significant potential and shortest payback times. Feel free to contact us for guidance in addressing your unique needs.
In our next post in this series, we'll dive deeper into fractionator overhead condensers and the options available to refineries. To be notified when a new blog entry drops, sign up for our mailing list and receive notifications.
Why Compabloc?
There are more than 500 Compablocs installed around the world working as cooling water exchangers in crude oil refinery, saving millions of gallons of cooling water every year.
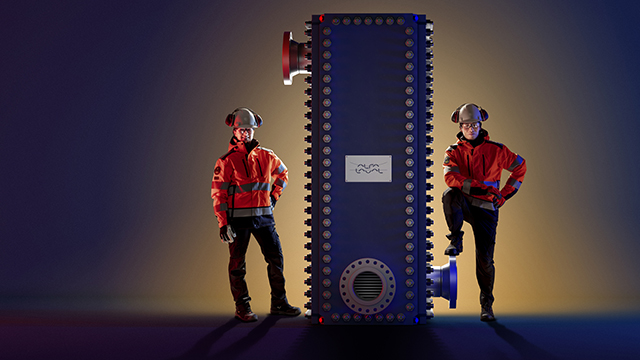
Read other relevant refinery blog posts
How to cut your refinery cooling water consumption by 30-50%
Reduce carbon intensity while improving bottom line in the refining sector
Overcome the challenges of cooling desalter water effluent
Debottleneck naphtha hydrotreaters with highest project ROI
Refinery alternatives to box coolers
Reducing energy consumption in industrial refrigerant systems
Benefits of Compabloc technology versus shell & tube
Using Packinox heat exchanger for catalytic reforming
Efficient wastewater cooling and reuse
Enabling sustainability goals of renewable fuels projects
Reducing scope emissions at refineries: A closer look into utilizing energy efficiency profitably
Energy efficiency opportunities around different heat exchanger positions in a fractionator – Part 1