Debottleneck naphtha hydrotreaters
Debottleneck NHT with highest project ROI
Naphtha hydrotreating (NHT) is one of the critical processes in a crude oil refinery. It removes sulphur and nitrogen compounds from naphtha to avoid poisoning of catalysts in downstream isomerization and reforming processes. Naphtha hydrotreating is a highly energy intensive process where charge (feed naphtha combined with hydrogen) is heated to a high temperature with the help of a heater before entering the reactor bed. To minimize overall energy input and emissions in the NHT, heat from the reactor effluent is exchanged with incoming charge in a combined feed to effluent heat exchanger (CFE).
Figure 1: Naphtha Hydrotreater reactor section generic flow diagram.
We can say that naphtha hydrotreater is a bridge between the atmospheric distillation unit and downstream gasoline conversion processes. A bottleneck in the NHT could undermine the refiner’s capability to maximize gasoline production. Some of the NHT de-bottlenecking projects we’ve supported in recent years have common themes; their drivers and challenges are summarized in the following chart:
Capacity in existing process units is often limited by either reactor heater or recycle compressor capacity. Designing the process with maximum energy recovery at a lower circuit pressure drop in the combined feed/effluent exchanger, offloads the heater and the compressor, enabling the increase in unit capacity. With Alfa Laval Compabloc heat exchangers in your NHT combined feed/effluent exchanger services, you can lower capex and decrease your footprint and lead time without having to invest more in the capacity of your fired heater or compressor. Projects implementing Compabloc solution in NHT have significantly improved a project’s ROI and it’s rapidly becoming a norm for industry leaders.
In one of our recent NHT debottlenecking projects for a US Mid-West Refinery using a Compabloc solution, their plant engineers were able to increase capacity by 40% at a fraction of earlier project estimates which were based on a conventional design solution. This refinery was changing their crude slate to add more light crude and thereby increasing the load on their NHT unit. During the feasibility study, they found the reactor heater was limited in capacity and needed replacement—a capital-intensive solution also involving emission permit reapprovals. Another idea to avoid investing in a higher capacity heater was to increase heat recovery in combined feed to effluent heat exchanger before the heater. However, they found it was not economically and practically feasible (plot space limited) as it would require 14 shell and tube delivering 13F internal pinch to coverup for existing heater capacity limits.
However, having learned from the success of their gulf coast sister refinery which had implemented Compabloc technology in a similar NHT debottlenecking project, they contacted Alfa Laval to optimize a Compabloc solution. With the right CFE design skills, process and application know how and operational experience, Alfa Laval proposed a Compabloc solution with just two units capable of delivering the required 13F pinch at a fraction of previous project estimates and in a much smaller footprint. The table below gives a summary of the driver, challenges and solution:
To gain more in-depth knowledge on how to implement Compabloc technology in NHT, we recommend tuning into our technical webinar, “Improving hydrotreater performance using welded plate heat exchanger,” and reading our technical articles below.
Click here for more information or contact an Alfa Laval refinery expert today.
Download our technical articles
Catalytic hydrotreatment
Hydroprocessing is becoming increasingly important for maximizing refinery profitability – either as a means of removing impurities before further downstream processing, or for securing a supply of products that meet stricter environmental regulations.
Improving hydrotreater performance with welded heat exchangers
Looking to improve your hydrotreater performance? Watch our recently recorded webinar where our refinery experts discuss why today’s hydrotreaters are facing challenges and how to solve them using welded plate heat exchanger technology.
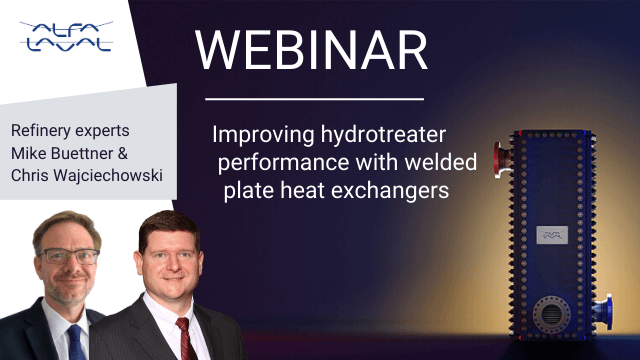
Read other relevant refinery blog posts
How to cut your refinery cooling water consumption by 30-50%
Reduce carbon intensity while improving bottom line in the refining sector
Overcome the challenges of cooling desalter water effluent
Debottleneck naphtha hydrotreaters with highest project ROI
Refinery alternatives to box coolers
Reducing energy consumption in industrial refrigerant systems
Benefits of Compabloc technology versus shell & tube
Using Packinox heat exchanger for catalytic reforming
Efficient wastewater cooling and reuse
Enabling sustainability goals of renewable fuels projects
Reducing scope emissions at refineries: A closer look into utilizing energy efficiency profitably
Energy efficiency opportunities around different heat exchanger positions in a fractionator – Part 1