Selecting the Right Service Partner for Your Plate Heat Exchangers
Regularly cleaning and servicing your plate heat exchangers helps to restore them to optimal condition and minimize maintenance downtime. But to realize these benefits, it’s important to have and stick to a planned, regular maintenance schedule—and finding the right partner can help
DATE 2024-02-27Cleaning, maintaining and servicing your heat exchangers on a regular basis will ensure minimized downtime and disruption to production lines and business operations. It keeps your equipment performing to the original design performance, ensuring that it’s as reliable as the original manufacturer’s specifications.
But this means keeping on top of a regular maintenance schedule. Even if your unit allows for in-line cleaning, all heat exchangers lose performance over time and full reconditioning is necessary at a certain point. In some cases, the unit may need repair, refurbishment or replacement of components such as plates, gaskets, bolts, connection linings or other frame parts.
Why consider a service partner for heat exchanger cleaning?
Even if you proactively clean your heat exchangers, the cleaning schedule might not be optimized to specific equipment or applications. You might also rely on the manufacturer you purchased the equipment from—and while they may be able to service their own brand, they aren’t necessarily capable of servicing the other brands you’re using (and may not have the parts on hand for repairs).
That’s why it makes sense to partner with a one-stop-shop organization that can clean, maintain and optimize your plate exchangers—regardless of brand. But how do you go about choosing the right partner? When doing your due diligence, ask these questions:
- Does the partner have the ability to clean all manufacturers’ heat exchangers or just their own brand?
- Do they have facilities across North America?
- What are their hours of operation and how responsive are they?
- Do they just clean, or can they recondition and even repair?
- Do they have tools that can show you how often you should be cleaning?
- Do they have tools that optimize the performance of the heat exchanger when your process demands have changed?
5 key benefits of finding a partner for heat exchanger services
1. One partner to service them all: Having one partner that can service any brand and serve as a one-stop shop for reconditioning makes it easier, safer and often more cost-effective to service your heat exchangers. For example, while Alfa Laval produces a wide range of branded heat exchangers, we can also recondition any brand, including AGC, API Schmidt, Arsopi, Bell & Gossett, Bretten, Fischer, Funke, Hisaka, ITT, Kapp, Kelvion, LHE, Reheat, Sondex, SPX, Swep, Tranter and WCR.
2. Depth and breadth of expertise: A partner with expertise across brands can help you get the most out of your plate exchangers, particularly if they need repairs. At Alfa Laval, we’ve been developing plate heat exchanger technology for 90 years and have accumulated an expansive portfolio of products and replacement parts. In many cases, we can improve the performance of non-Alfa Laval heat exchangers by replacing original components with Alfa Laval components and reconditioning processes.
3. Dedicated support: Look for a partner that has a network of support and knowledgeable experts on staff. At Alfa Laval, we have an expansive network of plate heat exchanger service centres across Canada; more than 20 factory-trained field technicians, service representatives and authorized service providers; as well as a centrally located distribution centre that supports you with parts and expertise, wherever you are, whenever you need it.
4. Advanced tools and technology. If you’re guesstimating when your heat exchangers need cleaning or reconditioning, the latest technology can help. Alfa Laval’s proprietary GPredict tool, for example, provides precise calculations based on your specific equipment and relevant application details, including temperature, gasket material, whether you use glued or non-glued gaskets and how often you open your unit in the course of annual operation.
5. Service agreements for worry-free support. The right partner can help you maximize performance and reduce operating costs through tailored support. For example, Alfa Laval can work with you to integrate our services into a Service Agreement for predictable and worry-free operations—minimizing the risk of unexpected breakdowns while giving you full control over your maintenance budget.
Find out more about how partnering with Alfa Laval can help you keep your heat exchangers in tip-top shape.
Plate Heat Exchanger Maintenance Manager Handbook
Are your plate heat exchangers functioning at optimal levels? Learn how to get more out of your plate heat exchanger in our Maintenance Manager Handbook.
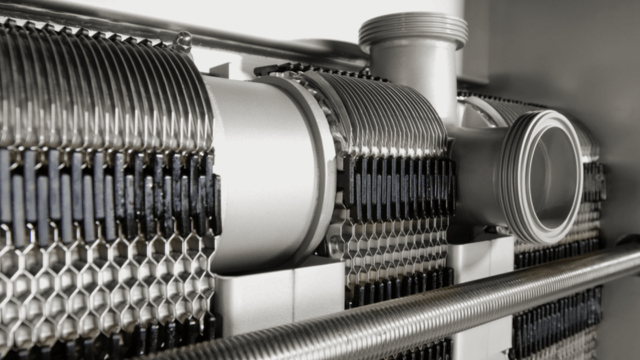
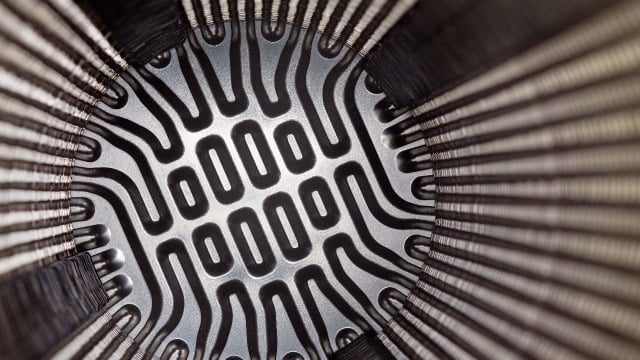
Contact Service and Parts
Toll free: +1 888 253 2226 (888-ALFACAN)
Service and Parts: canada.parts@alfalaval.com
Equipment Inquiries: alfacan.info@alfalaval.com
24/7 and Field Service
+1 888 253 2226
Alfa Laval Subject Expert: Gina Smith
Field Services Coordinator Ext. 343
Email us a Field Service Question
Service Centre (Eastern Canada)
Phone: +1 416 299-6101
Fax: +1 416 297-8690
101 Milner Avenue
Scarborough, Ontario
M1S 4S6, Canada
Service Centre (Western Canada)
Phone: +1 780 413-6349
Fax: +1 780 450-6747
6344 Roper Road
Edmonton, AlbertaT6B 3P9, Canada