Custom high-speed centrifugal separator powers reliability for leading utility company
In the energy industry, reliability is critical. Any downtime impacts customers — and could impact the grid.
DATE 2024-02-27Something as simple as water and fine particles can cause operational slowdowns and unplanned outages for electrical generation units — unacceptable in an industry that supplies such an essential service to citizens.
Bryan Texas Utilities is a municipally owned electric utility company operating in both urban and rural areas of three counties in central Texas. It’s the fifth largest municipal utility in the state, and one of only four in Texas to receive national recognition as a Diamond-Level Reliable Public Power Provider from the American Public Power Association.
Maintaining that reliability means maintaining its gas-fired steam turbine—right down to the lubricating oil.
“For us and for a lot of other plants, the oil is the blood of the turbine. If you don’t have good quality oil, you’re going to have major issues elsewhere. So it’s extremely important that we keep our oil in top shape.”
NICHOLAS COOK,
Division Manager of Production,
Bryan Texas Utilities
The Issue
An Alfa Laval centrifugal separator was put into service in the late 1970s to improve the performance of the company’s steam turbine. The separator continuously removes water and solid impurities from the lubricating oil to prevent contamination, improve the performance of the machinery and help reduce maintenance costs. Over the years, as the equipment aged, various parts were replaced or rebuilt.
When the centrifugal separator broke down in 2020, it was so old that Alfa Laval was no longer producing parts for that particular model. “We were looking at sourcing third-party parts—and the cost of those parts was going to be more than an entire replacement,” said Cook. “So we recognized that it was time to move to something more modern.”
But they also knew they wanted to replace the original centrifuge with another Alfa Laval unit.
“There was proven performance from the previous model that we’d used for 50-plus years so we knew we could trust this brand.”
But they couldn’t buy a standard centrifuge. Since the unit would have to pass through a narrow door and passageway, it would need to be customized so it could be installed without having to “bust through a brick wall,” said Cook.
The Solution
After Bryan Texas Utilities contacted Alfa Laval, they were connected with Separation Equipment Company, an Alfa Laval distributor that could customize the centrifuge to their particular specifications.
“We sent them drawings, data sheets and pictures of the existing unit to make sure we were going to be able to process the same volume of oil that we had in the past,” said Cook. “After we decided on the base centrifuge, we then started looking at our options. Modern centrifuges have heaters to help heat the oil before it’s processed, which was something we didn’t have with the original unit and would give us better performance out of it.”
The process was simple, he said, and Separation Equipment Company sent photos as the unit was being built, keeping Cook and his team updated on what was going on. They also received a set of videos demonstrating how the unit works, so they could train their operators ahead of time.
“That’s why we’re here: to problem-solve for the customer, to make modifications or customize. In this case, there was a 31-inch opening for the door, so we made the unit 30 inches wide,” said Floyd Goble, Sales Manager with Separation Equipment Company. It took less than three months—from purchase order to shipping—to design and fabricate the customized unit.
The Result
An oil analysis was taken shortly before the new centrifuge was installed, which showed elevated phosphorus levels that had resulted from their three-month downtime. This suggested phosphate ester (EHC fluid) contamination or contamination from a phosphorus-containing oil. After running the new centrifuge, levels have returned to normal ranges.
The new motor is much more energy efficient, but reliability was the company’s No. 1 priority.
“This is a ‘no news is good news’ scenario,” said Cook. “There haven’t been any work orders for servicing. I haven’t had to approve any parts purchases or replacements. So far all we’ve had to do is the regular maintenance. It’s something we don’t have to worry about it—just set it and forget it.”
A high-speed centrifugal separator can handle the large cleaning volumes required by Bryan Texas Utilities—with less maintenance, more uptime and an overall low total cost of ownership. It also provides the reliability that a nationally recognized power provider requires.
“Having the newer version of this centrifuge lets us run it with confidence, knowing we’re going to have consistent availability,” said Cook. “And that’s going to keep our oil in great shape and keep the rest of the plant reliable—hopefully for another 40 or 50 years.”
Contact Alfa Laval today, and we’ll set you up with an expert who can help you choose the right solution for your needs.
Is dirty lube oil costing your facility time and money?
Proper lube oil management and maintenance can offer benefits such as reducing downtime, increasing profitability and prolonging your equipment’s lifespan. Are you giving your lube oil the care it needs?
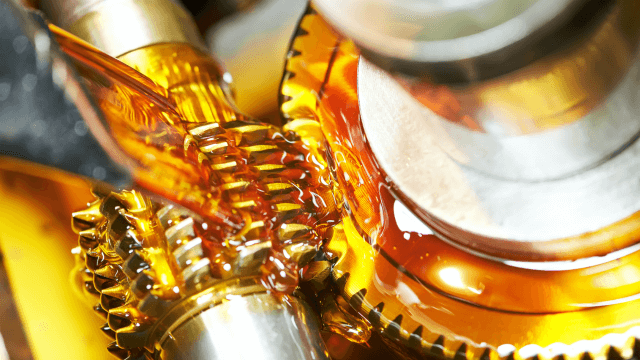
Talk to Our Experts
Nils Johansson, North America
+1 804 236 3110
Email Nils
Joshua Kowalchuk, AB, SK, MB,
+1 587 643 5505
Email Joshua
Derek Gluschenko, BC, Marine Separators, Service
+1 604 734 2225
Email Derek
Pierre Gosselin, QC, service d'équipement de séparation
+1 450 466 1120
Écrire à Pierre