Rethinking sustainable bio-based chemicals
Renewable chemicals, derived from biomass sources like plants and waste, are replacing fossil fuels in the chemical industry. Discover how this shift towards a circular economy minimizes waste and reduces greenhouse gas emissions.
DATE 2024-10-03Renewable chemicals, also known as green or bio-based chemicals, are slowly replacing fossil-derived ones. They’re derived from various biomass sources, such as trees, plants, crops, algae, bacteria and biological waste, producing a wide range of bio-based chemicals, fuels and products.
Since these biomass sources are renewable, they contribute to sustainable business practices, helping to lower greenhouse gasses and reduce dependency on non-renewable resources like fossil fuels. They play a key role in transitioning to a circular economy, in which the entire product lifecycle is designed to minimize waste and eliminate pollution.
Optimize the upgrading process of your pyrolysis products
Learn about Alfa Laval’s sustainable solutions for upgrading and optimizing pyrolysis products and advancing chemical circularity.
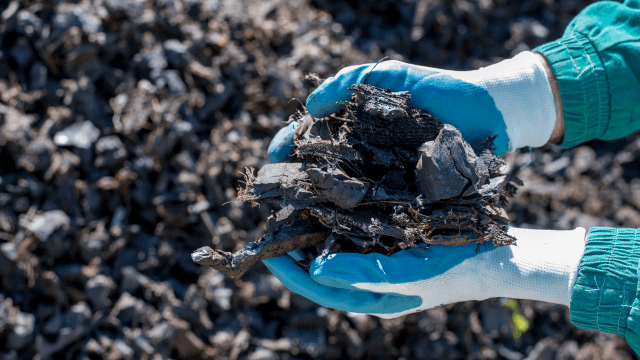
The shift towards bio-based chemicals
The chemical industry is still heavily dependent on fossil fuels and other raw material-based resources, but it’s undergoing a major shift. In a report on meeting the global need for carbon as a feedstock in the chemical and derived materials sector, nova-Institute estimates that recycled sources are estimated to account for more than 50 percent of the carbon embedded in chemicals and derived materials by 2050
While the energy sector is focused on decarbonization, it’s not possible to decarbonize chemicals. The path to sustainability and a net-zero chemical industry hinges on renewable chemicals, including the use of CO2-based and bio-based resources. Recycling technologies, which can handle plastics and tires and produce useful pyrolysis oil and other contaminated waste streams, also play a key role.
Bio-based chemicals offer a range of sustainability benefits, including reducing greenhouse gas emissions and driving the circular economy. But sustainability goes beyond environmental stewardship: by reducing dependency on fossil fuels, it provides diversification of feedstocks, which helps create more resiliency for companies and industries dependent on the use of chemicals. In addition, advances in technology are driving new production methods for renewable chemicals that optimize manufacturing processes.
Types of renewable chemicals
Renewable chemicals have a wide range of applications across industries, including industrial, pharmaceutical, agriculture, transportation and consumer goods. These include (but aren’t limited to):
- Biopolymers such as polylactic acid (PLA), polyhydroxyalkanoates (PHA) and bio-based polyethylene
- 2G Ethanol and methanol from Agri waste
- Acids such as acetic acid and glycolic acid
- Ketones such as acetone and methyl ethyl ketone
Biopolymers are plastic materials produced by industrial fermentation of renewable biomass sources that are easily biodegradable (as opposed to fossil starting materials). They serve as a renewable alternative to traditional plastics. Alcohols, acids and ketones can be used in the production of other products, while specialty chemicals—such as bio-based solvents, lubricants and surfactants—can be used in a wide variety of industrial applications.
Taking ethanol production to the next level with agri-wastes
Using Alfa Laval’s advanced process equipment, the next generation of bioethanol is being produced by fermenting biological feedstock materials such as sugarcane and starch crops. Some ethanol production plants have also started using biomass such as cellulosic fibers from crop residues, wood residues, dedicated energy crops and industrial and other waste products. Ethanol can be used in its pure form or as an additive to gasoline, increasing octane and reducing emissions.
Optimizing pyrolysis for biofuels and plastics
Biopolymers can replace conventional petroleum plastics, helping to drive the circular economy. While the concept isn’t new, biopolymer production has grown since recent EU directives aimed at reducing single-use plastics.
Virtually any source of biomass or waste can be used for pyrolysis, a thermal process in which materials decompose at an elevated temperature in an inert, oxygen-free atmosphere. As a result, it’s an increasingly popular solution for the renewable and recycling market.
Through pyrolysis, plastics, tires and residual materials from wood production are converted into oil, which is then refined into renewable low-carbon biofuel. Pyrolysis can also recover oil from recycled plastics, which is used as a chemical feedstock to create new plastic products. Carbon black can be recovered from recycled tires, which has significant economic and environmental benefits (new tires consist of 40% carbon black).
Types of renewable chemicals
Renewable chemicals have a wide range of applications across industries, including industrial, pharmaceutical, agriculture, transportation and consumer goods. These include (but aren’t limited to):
- Biopolymers such as polylactic acid (PLA), polyhydroxyalkanoates (PHA) and bio-based polyethylene
- 2G Ethanol and methanol from Agri waste
- Acids such as acetic acid and glycolic acid
- Ketones such as acetone and methyl ethyl ketone
Biopolymers are plastic materials produced by industrial fermentation of renewable biomass sources that are easily biodegradable (as opposed to fossil starting materials). They serve as a renewable alternative to traditional plastics. Alcohols, acids and ketones can be used in the production of other products, while specialty chemicals—such as bio-based solvents, lubricants and surfactants—can be used in a wide variety of industrial applications.
Taking ethanol production to the next level with agri-wastes
Using Alfa Laval’s advanced process equipment, the next generation of bioethanol is being produced by fermenting biological feedstock materials such as sugarcane and starch crops. Some ethanol production plants have also started using biomass such as cellulosic fibers from crop residues, wood residues, dedicated energy crops and industrial and other waste products. Ethanol can be used in its pure form or as an additive to gasoline, increasing octane and reducing emissions.
Optimizing pyrolysis for biofuels and plastics
Biopolymers can replace conventional petroleum plastics, helping to drive the circular economy. While the concept isn’t new, biopolymer production has grown since recent EU directives aimed at reducing single-use plastics.
Virtually any source of biomass or waste can be used for pyrolysis, a thermal process in which materials decompose at an elevated temperature in an inert, oxygen-free atmosphere. As a result, it’s an increasingly popular solution for the renewable and recycling market.
Through pyrolysis, plastics, tires and residual materials from wood production are converted into oil, which is then refined into renewable low-carbon biofuel. Pyrolysis can also recover oil from recycled plastics, which is used as a chemical feedstock to create new plastic products. Carbon black can be recovered from recycled tires, which has significant economic and environmental benefits (new tires consist of 40% carbon black).
Alfa Laval’s high-speed separation technology and plate heat exchangers can improve pyrolysis oil quality and yield. Find out more in our eBook on renewable chemicals.
The Alfa Laval advantage
Whatever your bio-based processes require, Alfa Laval’s extensive range of process equipment and expert knowledge of filtration and separation can help you meet your goals. We’ll assist in matching the right equipment to your process, your organism selection, your feedstock and your fermentation for successful production.
Alfa Laval can support you with separation solutions to suit every possible combination of circumstances and requirements. And our efficient evaporation systems, which minimize water usage and energy consumption, can be optimized for your specific circumstances including efforts in achieving Zero liquid discharge.
Partnering with an experienced and knowledgeable partner is key to driving sustainability. At Alfa Laval, we have extensive experience and application knowledge with bio-based chemicals. We can provide training and in-depth support for everything from basic separation tasks to those involving highly complex liquids and solids to achieve the highest yields.
Combined with our worldwide service network, you can count on reliable, high-quality and sustainable operations throughout the long lifetime of your equipment.
Learn more about bio-based chemicals or contact one of our pyrolysis experts to learn how Alfa Laval’s solutions can help your business.