Prevent unplanned downtime with planned equipment maintenance
Are you prepared for when your plate heat exchanger breaks down unexpectedly? How long can you afford for that equipment to be out of service? Following a service maintenance plan can ensure your equipment is in optimal working condition to help avoid costly unplanned downtime.
DATE 2024-02-27Prevent unplanned downtime with planned equipment maintenance
If a critical piece of equipment breaks down in the middle of a production run, it takes time to fix—and time is money. These days, with supply chain disruptions and shortages of critical components such as semiconductors, getting a spare part isn’t as easy as it used to be. Sometimes, you could be waiting days, weeks or even months to get something fixed.
In manufacturing environments, maintenance costs are estimated to be between 15% to 70% of the cost of goods produced, with about one-third of those costs being avoidable, according to the National Institute of Standards and Technology (NIST). Across industries, 82% of companies experience at least one incident of unplanned downtime—and often two or more—over a three-year period. It’s estimated that this costs industrial manufacturers up to $50 billion annually.
When it comes to critical equipment like plate heat exchangers, a lack of regular maintenance can result in fouling and contamination, which causes the equipment to underperform and could lead to long-term damage. Whether you do your own maintenance or rely on a service provider, routine checks can ensure that you catch and mitigate small issues before they become much bigger ones.
Planned vs unplanned downtime
Unplanned downtime occurs when equipment fails or breaks down—and if it happens in the middle of production or during a busy period, that downtime could be highly disruptive and costly to the business.
Regularly scheduled maintenance of tools, equipment and machinery will help to restore and extend equipment performance, which is why industrial manufacturers typically schedule plant downtime. They will select a time when disruption to operations will be minimal.
However, even if equipment is well maintained, there’s always a chance of unplanned downtime, such as a major storm or cyberattack. But unplanned downtime should be an exception, not the norm.
Often, unfortunately, unplanned downtime could have been easily prevented.
“The reality is that most manufacturing equipment generally fails in predictable ways with significant early warning if one knows how to look for it. Leading indicators that occur early in the failure cycle can typically be used to avoid catastrophic failure altogether,” according to Processing Magazine.
Unplanned downtime can have a trickle-down effect across the organization. The breakdown of a critical piece of equipment could hold up an entire production line, which in turn delays the delivery of goods and impacts customer satisfaction. If it needs to be repaired or restored by a service provider, that could take additional time—leaving you without critical equipment.
Why you need a service maintenance plan
Equipment maintenance should take place during planned downtime. But how often should a piece of equipment be serviced? Too much downtime isn’t a good thing, either.
The answer will depend on the equipment, its application and how critical it is.
For example, with plate heat exchangers, a maintenance schedule can vary widely depending on its operating conditions, from every six months to every year to once every several years. Therefore, a service maintenance plan should include recommendations on how long that piece of equipment should run before routine maintenance is required.
That plan should also include recommendations on which spare parts to keep in stock. Of course, not every organization chooses to—or needs to—keep parts in stock. In other cases, it may make sense to have a spare plate or even a spare unit on your production line, depending on the equipment's criticality and the parts' availability.
When you work with an Alfa Laval service advisor, we’ll create a service maintenance plan tailored to your operations, including recommendations for any spare parts you should keep on hand.
At Alfa Laval, we’re also committed to helping organizations increase their sustainability and reduce energy wastage. Want to learn more? Meet our Energy Hunters today!
Plate Heat Exchanger Maintenance Manager Handbook
Are your plate heat exchangers functioning at optimal levels? Learn how to get more out of your plate heat exchanger in our Maintenance Manager Handbook.
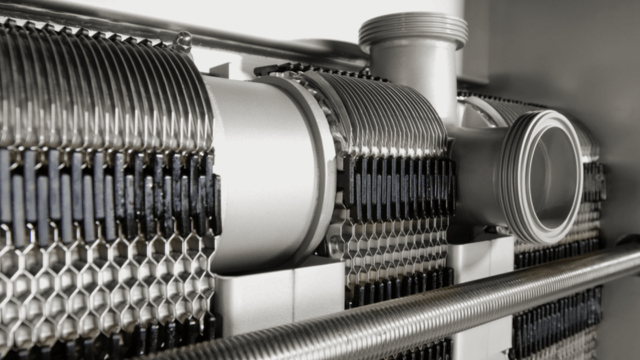
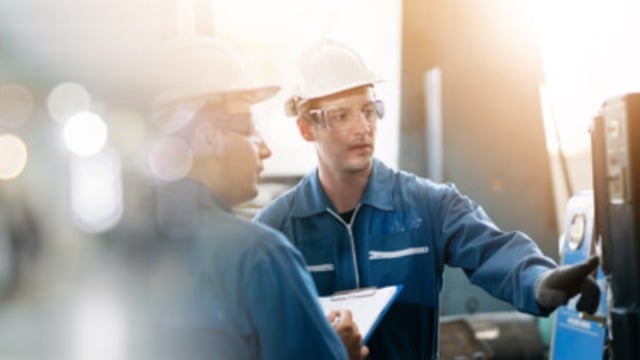
Contact Service and Parts
Toll free: +1 888 253 2226 (888-ALFACAN)
Service and Parts: canada.parts@alfalaval.com
Equipment Inquiries: alfacan.info@alfalaval.com
24/7 and Field Service
+1 888 253 2226
Alfa Laval Subject Expert: Gina Smith
Field Services Coordinator Ext. 343
Email us a Field Service Question
Service Centre (Eastern Canada)
Phone: +1 416 299-6101
Fax: +1 416 297-8690
101 Milner Avenue
Scarborough, Ontario
M1S 4S6, Canada
Service Centre (Western Canada)
Phone: +1 780 413-6349
Fax: +1 780 450-6747
6344 Roper Road
Edmonton, AlbertaT6B 3P9, Canada