Gain more than you think when you regularly service your plate heat exchangers
If you can’t remember the last time you cleaned your gasketed plate heat exchangers, they could be underperforming—or even contaminated. Reconditioning your equipment as part of a regularly scheduled preventive maintenance plan can help to ensure your heat exchangers are in optimal condition, minimize unplanned downtime and prevent unnecessary energy costs.
DATE 2024-02-27Gain more than you think when you regularly service your plate heat exchangers
Heat exchangers can often last years, even decades, if they’re well maintained. Wear and tear is normal for equipment in any industrial or manufacturing setting, but proactive, preventive maintenance can help to stop any issues—such as signs of corrosion or contamination—before they escalate into a larger problem.
Why heat exchangers lose efficiency over time
A heat exchanger creates a pressure drop and transfers heat between hot and cold fluids to strike the right balance in temperature. Without regular reconditioning, there’s a risk of underperformance, fouling and long-term damage to equipment.
To overcome the drop in pressure, a powerful pump is used to push liquids through the heat exchanger. However, if fouling has occurred, deposits will accumulate and create a higher pressure drop across the unit, which means it requires more pumping power—and more energy—to achieve the same result.
Depending on the nature of the transfer fluids and the application, heat exchanger performance may decline over a period of time due to the buildup of scale, sediment and/or debris on the plates.
As deposits form on the plate, it creates a barrier on the plate itself, decreasing thermal transfer efficiency. It’s similar to putting on a coat to go outside in cold weather; the coat creates a layer of insulation. But when it comes to your heat exchanger, you don’t want any insulation between the fluids and the metal.
How reconditioning can create efficiencies
Ideally, reconditioning should be done before complete fouling or process issues occur, which could result in irreversible damages. If a heat exchanger is reconditioned on a regular basis, it uses less pumping power to push the liquid through the heat exchanger and removes the build-up of deposits, providing better heat transfer.
Regular maintenance includes looking for signs of fouling, corrosion and leaks, especially at connection points. It should also include external and internal checks, such as tightening the frame and checking the status of gaskets, as well as cleaning the heat transfer area.
Maintaining your heat exchangers should be done during scheduled downtime. While there is a cost to regular maintenance, there’s a much higher cost if fouling or corrosion damages your equipment or results in an unplanned shutdown, which can cause delays, impact production and negatively affect ROI.
Ensuring your heat exchangers are operating in optimal condition can also save energy. Once a heat exchanger is restored to optimal condition, it uses less pumping power, which reduces energy usage and potentially contributes to reducing your plant’s overall carbon footprint. It can also help to lower ongoing maintenance costs and extend the lifetime of your equipment.
But there’s no one-size-fits-all maintenance plan for heat exchangers—it depends on the equipment itself and its application in your facility.
How Alfa Laval can help
Gasketed plate heat exchangers can be cleaned onsite or offsite. An Alfa Laval Performance Audit can help predict the optimal cleaning interval for your specific equipment and identify any areas where performance can be improved to ensure you’re getting the most from your heat exchangers.
Alfa Laval experts can also recommend cleaning solutions (depending on the specific heat exchanger and the application); provide cleaning services for both Alfa Laval and non-Alfa Laval plate heat exchangers; and conduct heat exchanger cleaning services on board or on-site.
Looking for even greater energy savings? Alfa Laval’s Energy Hunter program can help you save more by “hunting” for wasted energy across operational processes—helping to make your business more sustainable.
With our simplified tools, you’ll be able to estimate how much energy could be saved when using efficient plate exchanger technology, either by ensuring they’re serviced optimally or by recovering heat. Optimized service could save at least 8,000 kWh per year! You’ll also get a monetary value estimate, as well as a calculation of water consumption and carbon dioxide emissions reduction.
Find out more by talking to one of our heat exchanger experts today!
Plate Heat Exchanger Maintenance Manager Handbook
Are your plate heat exchangers functioning at optimal levels? Learn how to get more out of your plate heat exchanger in our Maintenance Manager Handbook.
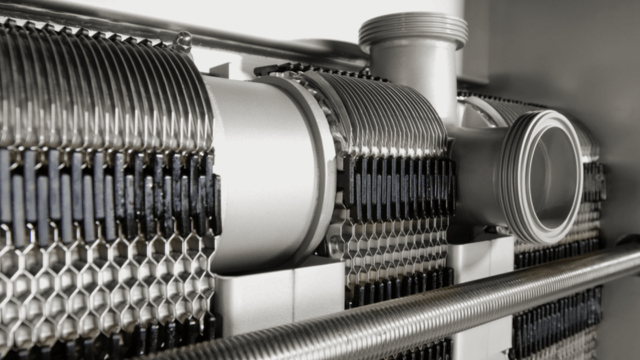
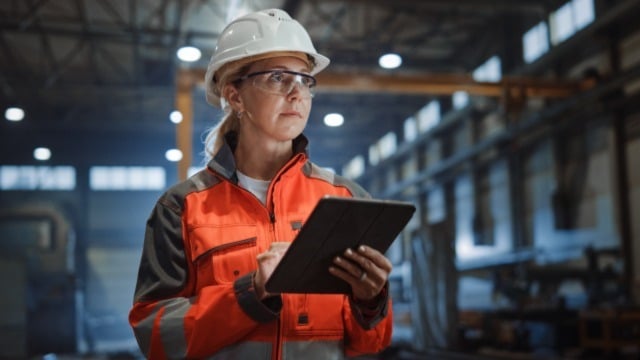
Contact Service and Parts
Toll free: +1 888 253 2226 (888-ALFACAN)
Service and Parts: canada.parts@alfalaval.com
Equipment Inquiries: alfacan.info@alfalaval.com
24/7 and Field Service
+1 888 253 2226
Alfa Laval Subject Expert: Gina Smith
Field Services Coordinator Ext. 343
Email us a Field Service Question
Service Centre (Eastern Canada)
Phone: +1 416 299-6101
Fax: +1 416 297-8690
101 Milner Avenue
Scarborough, Ontario
M1S 4S6, Canada
Service Centre (Western Canada)
Phone: +1 780 413-6349
Fax: +1 780 450-6747
6344 Roper Road
Edmonton, AlbertaT6B 3P9, Canada