Powering excellence: Plate heat exchanger insights in the Canadian energy sector
Canadian provinces are leading the energy sector and plate heat exchangers play a crucial role in their processes. Based on the findings of our industry survey, this blog will explore how these energy leaders use, service and maintain their heat exchangers.
DATE 2024-08-05An abundance of natural resources shapes Canada’s energy industry; from Alberta’s oil sands to Quebec’s hydroelectric power plants, Canadian provinces are leaders in the energy sector. In 2022, around $245 billion dollars of Canada’s gross domestic product was contributed directly by the energy sector, with crude oil making up 44% of the energy produced in Canada.
Plate heat exchangers play a crucial role in energy and power plants by facilitating efficient heat transfer processes, reducing energy consumption and optimizing thermal management across various operations. By taking a proactive approach to their maintenance, Canadian energy and power plants can enhance efficiency, reduce operational downtime and extend equipment lifespan.
In this blog, we’ll explore how some of those energy and power plants use, service and maintain plate heat exchangers.
Benchmarking insights for PHE maintenance and service
Learn how to maximize your heat exchangers' efficiency and minimize downtime in your facility. Download the research paper, "Optimizing Performance: Benchmarking Insights into Plate Heat Exchanger Maintenance and Service" today.
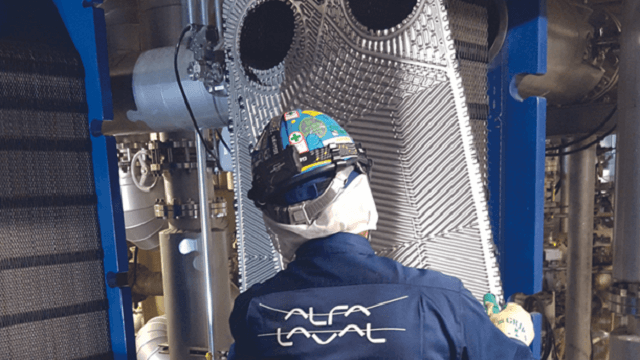
Who did we survey?
As part of our survey, we spoke to respondents in different roles within energy and power plants across Canada. The majority (40%) were in Quebec, followed by Alberta (21%). Ontario was third at 19%, followed by Manitoba (13%), British Columbia (4%) and Saskatchewan (2%).
In terms of job title, 28% of our respondents in the Power and Energy sector identified as Plant Operations Manager, while Plant Manager and Plant Engineering Manager were tied at 15% each. Maintenance Managers made up 11% of our respondents and 17% of those interviewed identified as being in the C-suite.
Heat Exchangers in Action
64% of our respondents currently use plate heat exchangers in their operations. In terms of specific usage, the majority (47%) use them for heating, 37% use them for heat recovery and 17% use them for cooling.
Energy and power companies often use plate heat exchangers in their plants for efficient heat transfer processes. Here are a few ways they might be used:
- Heat Recovery: Plate heat exchanges can be used to recover heat generated during processes such as oil refining, improving overall energy efficiency.
- Temperature Control: Cooling systems for power generation equipment such as turbines and engines use plate heat exchangers to transfer heat from the equipment and prevent overheating.
- Fuel Processing: In natural gas processing plants, heat exchangers help in heating natural gas streams for various processes like desulfurization.
- HVAC Systems: Energy and power plants often have extensive HVAC systems with integrated plate heat exchangers that help maintain both employee comfort and equipment operating temperatures.
Servicing Practices: A Breakdown
Regular servicing ensures your equipment performs to its original design and stays as reliable as the manufacturer intended. So, we asked our respondents how they were servicing their plate heat exchangers and whether they followed a specific schedule and methods.
Maintenance Practices:
- 80% adhere to specific cleaning and maintenance schedules
- 60% clean or service annually
- 20% of respondents clean or service every 1-4 years
- 3% of respondents clean or service every 5-7 years
- 17% of respondents were not sure
Factors Influencing Cleaning Frequency:
- 60% said performance changes drive cleaning
- 50% cited cost considerations as a primary influencer
- 43% said it depends on the types of fluid processed
- 40% follow regulatory requirements
- 30% take operating hours into account
- 27% follow the manufacturer’s recommended schedule
Cleaning Methods:
- 70% utilize high-pressure water jetting
- 50% opt for mechanical cleaning/brushing
- 47% utilize chemical cleaning
Cleaning Providers:
- 47% rely on the manufacturer
- 30% use a repair company
- 23% use a distributor
Performance Measurement Practices:
- 67% use continuous data logging to measure performance
- 27% measure performance randomly
- 7% say they do not measure performance
The Advantages of Plate Heat Exchangers
As a leading global supplier of products and solutions for heat transfer, you can count on Alfa Laval's products for their reliability, low operating costs and superior performance. Our solutions address the needs of energy and power plants across many categories, including:
Crude Oil Refinery
Energy efficiency improvement is one of the most important ways for refineries to reduce costs and Alfa Laval has a range of heat exchangers suitable for condensing vapours, cooling products and reboiling duties.
Nuclear Power
Cooling, heating, cleaning and separating fluids and gases are critical processes and Alfa Laval has the extensive knowledge, long-term experience and reliable, energy-efficient solutions nuclear plants need for safety, efficiency, cost control and uptime.
Accelerating Sustainable Solutions
Alfa Laval’s industry-proven and efficient heat transfer solutions help customers save energy, improve heat recovery and reduce carbon dioxide emissions through maximizing energy efficiency.
District Heating
Alfa Laval’s energy-efficient plate heat exchangers can support all district heating processes, reducing carbon emissions and the demand for primary energy at the same time.
District Cooling
Alfa Lava’s plate heat exchangers excel in district cooling, saving costs, enhancing energy efficiency, and providing superior cooling performance.
Achieve Operational Excellence with Alfa Laval
Alfa Laval’s heat transfer solutions save 100 GW of energy in industry every year—enough power to heat 20 million homes. And we’re relentlessly innovating toward more efficient and cleaner energy solutions.
Our expertise in heat transfer, separation and fluid handling for Canadian energy and power plants, as well as our reputation for reconditioning and repairing existing equipment, means we’re the ideal partner to help your existing (or future) plate heat exchangers reach peak performance.
To learn how Alfa Laval can help you maximize the efficiency and longevity of your plate heat exchangers or upgrade your equipment, contact one of our experts today.