Cool under pressure: Transforming petrochemical plants through innovative heat transfer strategies
Heat transfer is critical to every phase of the petrochemical process—from reaction to separation and cooling. For petrochemical processing plants, discovering how to optimize this process is a key step to boosting efficiency and productivity while meeting major sustainability goals.
DATE 2024-11-01Heat transfer is critical to every phase of the petrochemical process—from reaction to separation and cooling. For petrochemical processing plants, discovering how to optimize this process is a key step to boosting efficiency and productivity while meeting major sustainability goals.
With unique pressure and temperature demands, every plant has its own heat transfer requirements. But petrochemical processors can also face similar, significant challenges when it comes to achieving optimal heat transfer, such as:
- Insufficient cooling capacity: Higher ambient temperatures in warm weather can reduce the efficiency of cooling water systems, affecting overall process performance and resulting in lower production rates.
- Production bottlenecks: Inadequate cooling or heating capacity can limit the plant's entire production flow. The availability of cooling water can also cause bottlenecks, especially during peak demand periods or in warmer climates.
- Unnecessary fuel consumption and excess emissions: A lack of efficiency or optimization of the heating, cooling, condensing, re-boiling and heat transfer processes results in excess waste, greater energy consumption and higher costs, all at a significant price for the environment.
Implementing the right heat transfer technology can be the difference between success and continued inefficiency when it comes to addressing these challenges head-on and achieving your overall sustainability targets.
Alfa Laval has innovative heat exchanger solutions to help you reach these goals. We’re your partner in driving greater efficiency, sustainability and cost savings in your petrochemical business.
Clear bottlenecks in heating and cooling applications
Heat transfer bottlenecks in one area can often impact the entire plant. But you don’t need to expand your plant footprint to accommodate new equipment that addresses these problems. Upgrading your heat exchanger to a more energy-efficient option increases production and reduces carbon emissions. Alfa Laval offers compact sizes that allow you to save on installation costs and keep your existing structure.
By operating at closer temperature approaches, our heat exchangers use lower-grade steam, enhancing energy efficiency. Their compact design offers increased duty with the same cooling water capacity, eliminating the risk of production bottlenecks.
Boost cooling capacity
Whether you’re facing cooling limitations because of insufficient capacity or high ambient temperatures, insufficient cooling is a problem in petrochemical production that can often lead to lower production rates.
When cooling capacity is no longer enough, the simplest solution to increase production is upgrading your existing heat exchangers for a more efficient model. Compact, efficient heat exchangers from Alfa Laval allow petrochemical producers to work with higher temperatures, reuse waste heat in place of cooling and limit the production issues that result from insufficient cooling capacity.
Lower emissions and fuel consumption
Petrochemical producers aren’t just looking to boost efficiency and production yield—they’re under pressure to lower carbon emissions. Improving process sustainability is one way to achieve these targets.
By installing innovative heat transfer solutions that deliver high thermal efficiency, plants can boost performance, save energy and reduce CO2 emissions.
With Alfa Laval’s Compabloc heat exchanger technology, crossing temperatures in a single unit maximizes energy recovery, reduces power bills and boosts petrochemical plant performance. Its compact design delivers superior heat transfer, improved heat recovery and minimal fouling, resulting in superior thermal efficiency and energy savings.
Belgian petrochemical producer Dow Wolff chose Compabloc when it needed a solution to replace a broken shell-and-tube reboiler on its solvent recovery column.
The increased thermal efficiency enabled annual energy savings of 500 kW — and significant annual cost savings of over $130,000.
Sustainability is no longer an option for petrochemical processing plants—it’s a requirement to stay competitive and compliant. As an experienced partner, Alfa Laval provides heat exchangers that suit your needs at each phase of the petrochemical process while driving optimal performance and energy savings.
Contact one of our experts to learn more about how Alfa Laval’s petrochemical solutions can help your plant become more efficient, sustainable and profitable.
The future of petrochemical production
Download our free eBook to learn more about how Alfa Laval’s solutions can help your petrochemical plant improve efficiency at every stage of your process.
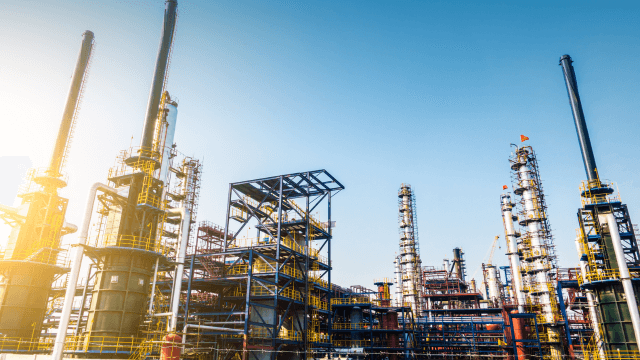