Sustainable energy solutions – Be an energy hunter to reduce your energy bill
To effectively reduce energy costs and contribute to a more sustainable environment, it is crucial to invest in a properly designed and high-performing heat exchanger. It is recommended to only consider units that have been third-party performance certified. This certification not only comes at no additional cost, but it also benefits your wallet and the environment.
At Alfa Laval, we have a wealth of experience in this area and can offer tailored sustainable energy solutions to meet your specific needs. We encourage you to contact your local Alfa Laval office or partner to learn more about how we can help you achieve your energy-saving goals.
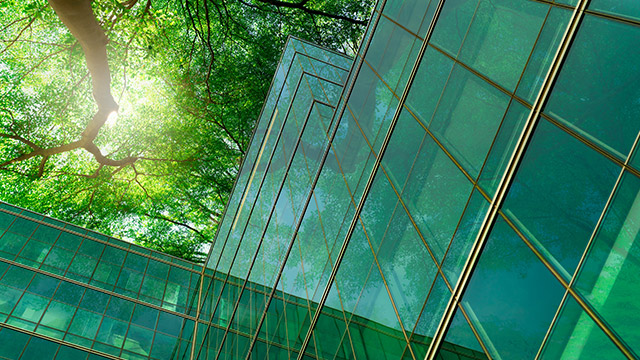
1. AHRI Performance Certified plate heat exchangers for sustainable buildings - Save energy, money and decrease the carbon emission
To ensure optimal performance, it is important to carefully consider the approach temperature specified when using plate heat exchangers as pressure breakers. Generally, this temperature should be quite low, around 1 or 2°C. However, if a plate heat exchanger is selected with tolerances that result in variations in approach temperature or pressure drop, the unit will underperform. This can lead to higher pumping costs or lower chiller operation temperatures, both of which can result in increased operational costs.
Fortunately, there is a solution that can help you avoid these issues and save money. By using AHRI Performance Certified gasketed plate heat exchangers, you can specify your exact requirements and be confident that you will get the performance you need. This will help you to minimize any negative consequences on chiller operation costs and ensure optimal energy efficiency.
Make sure to specify AHRI in your procurement documents:
State:
"The plate heat exchangers shall be AHRI certified in the AHRI Liquid to Liquid Heat Exchangers Certification Program (LLHE)”
Additional verification
”The PHE specs as selected, shall be verified and registered by AHRI before purchase"
Example
Chiller 3,000 kW COP5 running half of the year, cost of electricity at 0.2 €/kWh
(Cost of running the chiller 525,600 €/year with associated carbon footprint 1.0 kg CO2/kWh)
Typical
- 14°C->7°C
- 13°C<-6°C
Savings when avoiding underperformance of the gasketed plate heat exchanger:
Variable flow systems
- Avoid higher pump running costs (42 kW per pump, save up to 5,265 €/year and 26,200 kg CO2/year)
Fixed flow systems
- Avoid lower chiller evaporation temperature (3.5% savings, save up to 18,290 €/year and 91,980 kg CO2/year)
2. Chiller condenser protection
Chillers are known for being the most electricity-consuming equipment in HVAC installations, especially in warmer countries. One of the biggest contributors to escalating electricity costs is the accumulation of scale in water-cooled condensers. Regular cleaning is therefore essential to maintain optimal chiller performance and reduce operating costs. Additionally, isolating the chiller from the open cooling tower can result in energy savings of up to 20% over the system's lifetime.
At Alfa Laval, we have a solution that can help you keep your chiller condenser clean and minimize the need for maintenance and cleaning. By installing an interchanger with an AHRI performance certificate, you can ensure that your system operates at maximum efficiency, saving you money and reducing your environmental impact.
Example
Chiller 3,000 kW COP5 running half of the year, cost of electricity at 0.2 €/kWh
(Cost of running the chiller 525,600 €/year with associated carbon footprint 1.0 kg CO2/kWh)
Typical
- 36°C->30°C
- 35°C<-29°C
Savings with a condenser protection interchanger
- Avoid higher chiller condensing temperature and pressure (10% savings, save up to 52,500 €/year and 262,800 kg CO2/year)
- Avoid annual maintenance costs for condenser cleaning and damage to tubes
3. Save money, energy and decrease the carbon emission by turning the chiller off
By installing an Alfa Laval gasketed plate heat exchanger between the cooling tower and chiller condenser, you can completely turn off the chiller during the winter months. Instead, the fan coils can be supplied with cold water that is only 1°C above the temperature of the cooling tower. This can lead to significant energy savings and lower operating costs.
To achieve these benefits, we recommend installing a cooling tower interchanger with an AHRI performance certificate. This ensures that your system is operating at peak efficiency and that you are getting the energy savings you need to reduce your environmental impact and save money.
Example
Chiller 3,000 kW COP5 running half of the year, cost of electricity at 0.2 €/kWh (Cost of running the chiller 525,600 €/year with associated carbon footprint 1.0 kg CO2/kWh)
Typical
- 14°C->7°C
- 13°C<-6°C
Savings with turning the chiller off 30 days a year (360 h)
- Utilising the cool ambient temperature available from open cooling tower (8% savings, 360/4,380; save 42,048 €/year and 210,240 kg CO2/year)
4. Reduce cost and CO2 footprint with heat recovery in buildings with open cooling tower
Hospitals, hotels, and universities can significantly reduce fuel costs by recovering waste heat from their cooling tower systems. This heat can be repurposed to preheat boiler feed water, used for space heating, or to produce hot water for taps. With the latest technology, it is possible to recover heat from cooling tower water returns with a temperature difference as low as 1°C. This application not only saves on fuel costs but also reduces the load on the cooling tower.
To take advantage of these energy-saving opportunities, we recommend you map out the possibilities for heat recovery in your cooling tower system.
Example
Chiller 3,000 kW COP5 running half of the year, cost of natural gas at 0.2 €/kWh (Cost of running the chiller 525,600 €/year with associated carbon footprint 1.0 kg CO2/kWh)
Typical
- 36°C->16°C
- 35°C<-15°C
Savings with recovering waste heat from the cooling tower
- Recover the waste heat rejected at the cooling tower to preheat the boiler feed water
- Save on natural gas heating costs for tap water needed in hotels, hospitals, universities, and other public spaces
- Assuming 36°C cooling tower return temperature is available only 30 days in the year during summer 360 h/year (25m3/h or 600 kW water pre-heating savings, 21,600 €/year and 216,000 kg CO2/year)
5. District heating pressure breaker – reduce costs and carbon emission with focus on low return temperature
Efficiency and cost reduction are key challenges in all district heating networks. One effective way to achieve these goals is by designing and operating buildings that deliver the lowest possible return temperature from the heating system. When the return temperature is low, a higher delta T can be achieved on the district heating network, resulting in lower flow rates. This means lower pumping costs and reduced heat loss in the grid, enabling higher efficiency in heat production.
To achieve these benefits, we recommend specifying AHRI-certified heat exchangers. These heat exchangers are designed to perform as intended and can help you achieve optimal energy efficiency in your heating system.
Example
District heating network 3,000 kW heating, working with a delta T of 30°C and flowrate of 86 m3/hr, running half of the year, cost of electricity at 0.2 €/kWh
Typical
- With delta T of 30 °C
District heating loop 80°C->50°C
City heating loop 75°C<-45°C</br />
Savings with a higher delta T of even 2 °C will reduce the flow in the system
- With delta T of 32 °C
80°C->48°C
78°C<-45°C - New flowrate 80m3/h with lower return temperature
Save on pumping costs 10% less flow
4kW less pumping power - Energy savings 4kW x 4,380 h x 0.2 (Save up to 3,504 €/year and 17,520 kg CO2/year)
6. What is the ideal pressure drop to specify for gasketed plate heat exchangers in HVAC applications?
Pressure drop is the fuel/cost for heat transfer and is created by using electricity in pumps. How to use the available pressure in the most optimum way is the challenge for designers and consultants.
Reduce electricity cost by specifying a low pressure drop across the plate heat exchanger. The consequence is specifying an inefficient plate heat exchanger, which is operated at less then ideal conditions. Low turbulence, low velocities, and oversized. This leads to faster fouling and increase in operation costs.
The total lifecycle cost is a balance of pressure drop and plate heat exchanger, efficiency. The ideal pressure drop being 50-70kPa with a negligible effect on increased pumping costs. A building is only as efficient as the efficiency of the equipment in the plant room.
Click for a detailed pdf file: What is the ideal pressure drop to specify for gasketed plate heat exchangers in HVAC applications?
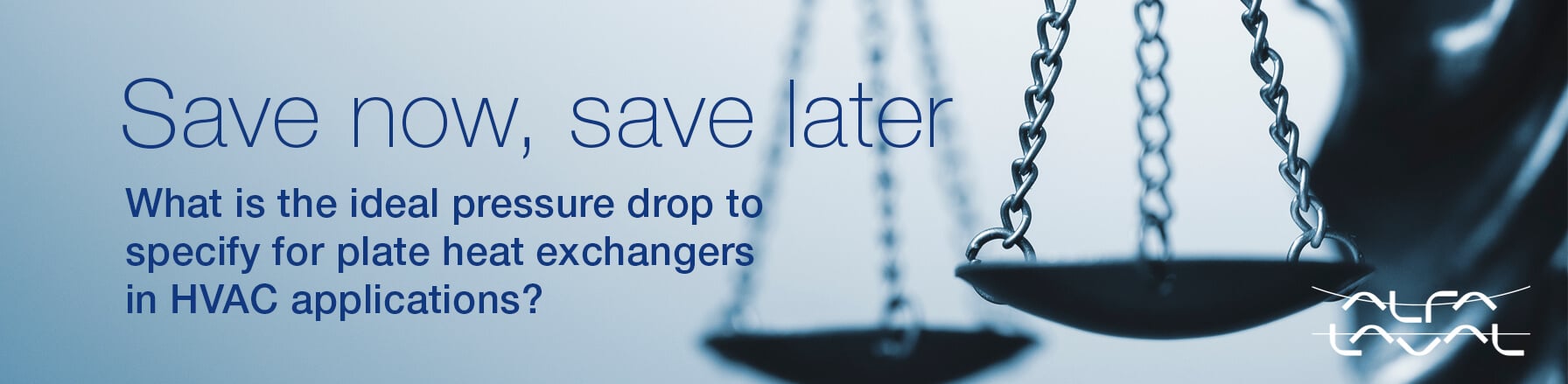
AHRI-performance-certified heat exchangers for confident thermal performance
Certification from the Air-Conditioning, Heating, and Refrigeration Institute (AHRI) is the only global third-party verification of thermal performance, giving you independent assurance that your plate heat exchanger will perform in accordance with the manufacturer’s published ratings. Alfa Laval offers AHRI-certified gasketed plate heat exchangers, brazed plate heat exchangers, and fusion-bonded plate heat exchangers.
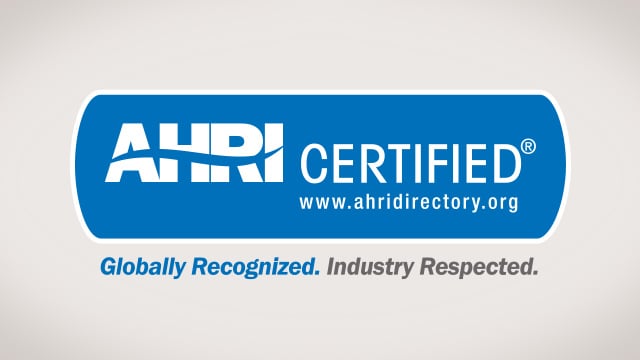
Making the world’s buildings more energy-efficient
Explore the benefits of our cutting-edge heat exchanger technology and stay updated with the latest industry trends and challenges in heat efficiency on our main page.
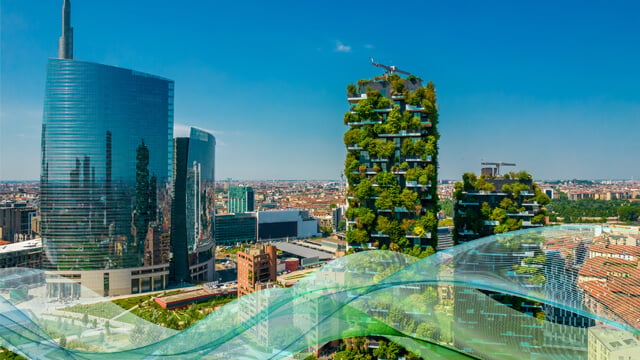